Lockout/tagout procedures are a core component of any lockout/tagout program. Clear, intuitive procedures help ensure authorized employees understand the safest ways to perform service and maintenance on machines and equipment. This helps protect workers from injury by unexpected re-energization or release of stored energy while working on machines and equipment.
What are Lockout/Tagout Procedures?
Protect Employees with Lockout/Tagout Policies and Procedures
Lockout/tagout procedures are written steps used for affixing lockout or tagout devices to energy isolation devices to bring a machine to a zero-energy state, the point at which the equipment has been safely isolated from any chances of re-energization or release of internal contained energy. Stated plainly, it’s when everything has been shut off completely.
Machine-specific lockout/tagout procedures guide an authorized employee through a sequential process that renders a piece of equipment safe to maintenance.
For production facilities based in the United States, adherence to compliance requirements for lockout/tagout procedures is managed by the Occupational Safety and Health Administration (OSHA). By partnering with employers and safety specialists, OSHA has led the way in dramatically reducing workplace deaths.
Are you and your company adequately prepared with fully developed lockout/tagout procedures? Could you use some guidance on OSHA lockout/tagout regulations? Our team of safety engineers provides consultation and guidance for procedure creation and documentation for machines of all types.
Want more LOTO procedures information? Learn about equipment exemptions, authorized employee requirements, procedure documentation and more in this must-read eBook.
Benefits of Lockout/Tagout Procedures
Just as lack of controls and lack of employee training can lead to a dangerous workplace, the adoption of safety and risk management best practices can help manufacturers keep employees safer and be more productive. According to LNS Research, companies that implement safety-related best practices perform better when it comes to delivery, equipment effectiveness and incident rates.
Lockout/tagout procedures, in conjunction with a hierarchy of administrative controls that influence the way employees work, can dramatically increase worker safety. Those controls include policy changes, documented procedures, or various forms of training. These changes actively help prevent accidents in the workplace.

Improved Worker Safety
Developing and implementing a lockout/tagout program, complete with written procedures and training, can help prevent many lost-time accidents. Compliant lockout/tagout procedures provide the needed information for employees to work safely on equipment and a good LOTO training informs authorized employees on related hazards and methods for control.

Streamlined Compliance
Compliance with state and federal safety regulations, including OSHA, should be a goal of all companies, regardless of size. Having documented lockout/tagout procedures that are both comprehensive and compliant will result in a safer workplace and reduced concern for safety violations or fines. In addition, workplace supervisors will know that they are doing all they can to provide a secure environment focused on safety and productivity.

Increased Productivity
Beyond improved safety and compliance, there’s a quantifiable productivity return on investment associated with lockout/tagout procedures. The procedures will allow your authorized employees to more quickly lockout equipment and restore it to service. That can result in more equipment availability, less time spent by the authorized employee, and also less equipment/process down time.
Components of Lockout/Tagout Procedures
Whether you are based in the United States and need to adhere to OSHA lockout/tagout regulations, or you are based elsewhere and are governed by national and regional safety regulations, it should be your goal to have compliant lockout/tagout procedures.
Lockout/tagout policies are the foundation of an energy control program. These policies provide the blueprint for lockout/tagout procedures and include: identifying who is responsible for developing and maintaining the program, outlining what type of procedures will be most effective, and documenting the training requirements.
Procedures are vitally important in the everyday safety of the employees of a company. Therefore, every procedure should contain clear and concise instructions and information as to how to lockout a specific piece of machinery.
The information required on each procedure, according to OSHA standards, is as follows:
- The scope, purpose, methods, and rules used for controlling energy
- The intended use of the procedure (lockout)
- Steps for shutting down the equipment
- Steps for isolating and controlling hazardous energy
- Steps for the placement and removal of lockout or tagout devices
- Steps for testing the machine to confirm it was properly locked out
We can help you create an effective lockout/tagout solution that results in productivity gains, decreased downtime and improved workplace safety.
Creating Machine-specific Lockout/Tagout Procedures
Lockout/tagout procedures must be developed for any machine with two or more sources of lockable and/or residual energy. Equipment that is not owned by the employer and not serviced by employees does not need a written procedure. Procedures are also not needed for simple, single-energy source machines. Specific exemption criteria can be found in the standard: 1910.147(c)(4)(i).
Lockout/tagout procedures should be machine specific. That is, a specific lockout/tagout procedure should be developed for each individual piece of equipment. The procedure should identify the following machine-specific information including description of machine, location, energy sources and methods of controlling those sources.
It may be possible to create a generic lockout/tagout procedure to be used on a group of similar equipment. When choosing to employ a generic procedure, care should be taken to only group equipment with the same energy source types and methods for isolation. Generic procedures should only be used for simple machines, with a maximum of two to three energy sources.
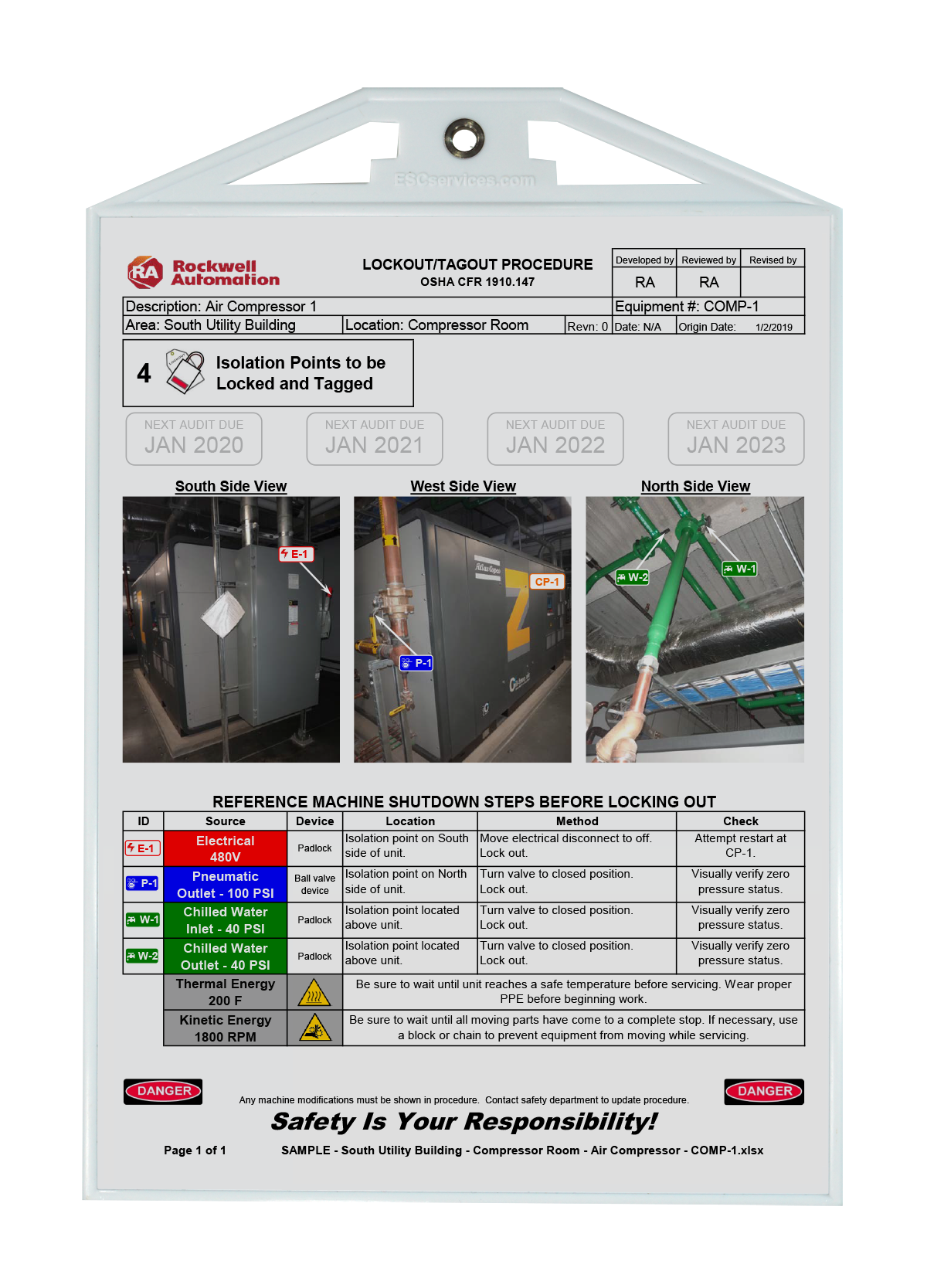
Annual Audits of Procedures
Identify and Correct Deficiencies: Ensure Employees Know Responsibilities
OSHA requires organizations to review procedures annually. An audit helps determine if the procedures are providing adequate protection to employees and if any changes are needed. It is also important to confirm that employees understand their responsibilities under each procedure and are able to follow steps properly.
An annual review of your lockout/tagout program is the perfect opportunity for employers to identify possible weaknesses in their program and help to ensure that all employees are safe from injuries resulting from the inadvertent energization of equipment. If the review is conducted thoroughly and with a focus on safety, employers can correct possible deficiencies before they result in consequences.
Rockwell Automation is a global leader in providing lockout/tagout services to a wide range of industries. Our experts can answer your questions about the auditing process and devise a review process to meet your needs.
Procedure Requirements for Authorized Employees
Performing maintenance or servicing equipment can be dangerous to employees, so only authorized employees are allowed to perform maintenance or servicing of equipment. OSHA clearly defines who is an authorized employee, the responsibilities of an authorized employee, and who is an affected employee.
By OSHA lockout/tagout standards, an authorized employee is a person who locks or tags out equipment to perform servicing or maintenance.
Authorized employees are required to attend training on applicable hazardous energy, types, and magnitudes in the workplace. In the training, authorized employees learn how to perform lockout/tagout while servicing or performing maintenance. They need to know the proper steps for isolating and locking out energy sources and should be trained on methods for verifying the accuracy of the lockout.
Also, authorized employees need to understand how to perform a group lockout, handle shift change, and know what to do in other, special circumstances.
The requirements for when a machine is required to be locked out include:
- If the employee is placing any part of their body into the equipment where work is being performed
- If any part of their body is in an associated danger zone
- If an employee bypasses a guard or other safety device, the machine must be locked out
- If an employee must do work on the equipment that is not routine, they are considered an authorized employee
Deviation from the written lockout/tagout procedure is strictly prohibited under OSHA’s Control of Hazardous Energy standard.