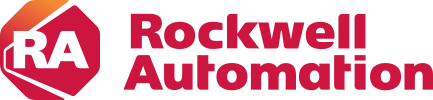
- Maintain consistent fill volumes
- Reduce product waste
- Respond to changing consumer tastes and packaging preferences
- Generate new sales and revenue opportunities
- New volumetric can filler and seaming system with Artificial Intelligence (AI)-enabled control that detects and autocorrects volumes outside the set point range
- Integrated safety control to help prevent unexpected operation and injury
- System features Rockwell Automation’s Micro850® programmable logic controllers (PLC), Compact GuardLogix® 5380 controllers, Compact I/O™ modules and HMI technologies, including PanelView™ 5000 Graphic Terminals
- Increased throughput
- Increased run speeds
- Improved fill accuracy to within a half percent of set point
- Increased flexibility to handle multiple can sizes with a variety of beverages
- Reduce manual interaction
- Improved operator protection
Challenge
While beer remains the most widely consumed alcoholic beverage in the world, market share has declined as the choice of both alcoholic and nonalcoholic options has grown. Meanwhile, like most businesses, brewers large and small have faced inflationary and supply challenges.
Flexibility, precision, and eliminating product waste is essential for brewers to manage these issues, including responding to changing consumer tastes and packaging preferences while generating new sales and revenue opportunities. To help meet these needs, TechniBlend™ launched a new volumetric can filler and seaming system, the ProFill V series. The Wisconsin-based OEM is a recognized leader in several industries including the beverage and brewing sectors.
Solution
Artificial Intelligence Delivers Precise Production and Eliminates Waste
With TechniBlend’s new system, brewers can accelerate production with run speeds between 100 to 600 cans a minute while achieving precise and consistent filling volumes. The ProFill V triples the level of filling accuracy compared to mechanical fillers enabling brewers to maintain volume within a half percent of their set point.
“Tighter volume control and improved accuracy reduces product waste. More product goes into the cans and less down the drain,” says TechniBlend’s Jon Breidenbach, manager-Filling Systems. “The system’s embedded artificial intelligence (AI) technology detects and autocorrects volumes outside the set point range as error correction algorithms monitor and optimize each filling valve’s performance.”
That precision and reduced waste is especially important as an increasing number of breweries pursue co-packing contracts in which they fill and package products for other brew and beverage customers.
Rockwell Automation Technologies are “The Brains of the System”
TechniBlend, which is an OEM member of Rockwell Automation’s PartnerNetwork™, developed the ProFill V system with a number of Rockwell Automation technologies.
“We lean toward Rockwell for its ease of use and feature rich products. They’ve been a very strong partner,” Breidenbach says. “A lot of our customers are already using equipment with Rockwell components so when we use Rockwell in our machines it makes it easier to pair them up and talk to other equipment across the processing line.”
The ProFill V series features Rockwell Automation’s Micro850® programmable logic controllers (PLC), which Breidenbach describes as, “the brains of the system controlling how much and automatically correcting volume with the AI logic we’ve programmed into those PLCs.”
Safety is also a major element with Rockwell Automation Compact GuardLogix® 5380 controllers and Compact I/O™ modules. TechniBlend plans to use the ProFill V as a test bed for integrated safety control and how it could be expanded to its other offerings.
“We’re constantly reviewing our beverage filling equipment and how we can provide a safer solution for packing line operators,” Breidenbach says. “The ProFill V has dedicated safety logic and interlocks that we’ve implemented across the board to help prevent any unexpected operation and injury. This is one of the safest machines we’ve developed.”
Local Brewer First to Install
A local craft brewing company based in Milwaukee, Wisconsin, was the first customer to use the ProFill V system. The brewery produces beers, seltzers, and canned waters for distribution in several midwestern states.
“This brewer wanted to increase production but had an older filler that ran a bit slower, so they were looking to upgrade to a more advanced system. They’re also getting into the co-packing market which gives them the opportunity to use the new filler to bring in more revenue,” explains Breidenbach. “What makes this brewery a great first customer is their variety of products, which allows us to demonstrate the system’s flexibility and versatility.”
The ProFill V is designed to fill cans in multiple sizes with a wide array of beverages and liquids. Quickly and easily, operators can make recipe-based changeovers with the system’s intuitive HMI technologies from Rockwell Automation, including PanelView™ 5000 Graphic Terminals.
Result
More Throughput; Less Manual Interaction
TechniBlend intentionally targeted a local customer for ProFill V’s first installation so service professionals could be onsite to provide extensive training and support during and after commissioning.
“We saw it as a learning opportunity for us both. The entire set up process was very smooth,” Breidenbach says. “The brewery has been able set speed and volume points based on the product running and just hit go. And with the system’s AI, it’s been pretty hands off for them so they can free up guys on the packing line to focus on pack out and get more product out the door.”
Since the brewer installed the ProFill V in spring 2023, it’s been able to increase run speed, record more consistent fill volumes, and increase throughput.
Increasing Automation and Ease of Use
Looking ahead at the “next round” of automation for the brewery, TechniBlend plans to focus on can heights. Currently, the brewer uses the ProFill V for 12 and 16 ounce cans but is exploring adding 19.2 ounce cans in the future. But, adjusting can heights remains a manual process in which operators raise the filler bolt to allow the cans to fit.
“We’re developing some equipment and programming logic to make that more of an automatic process so they can enter can height on the HMI and the machine would raise whatever is necessary to get up to that point,” explains Breidenbach. “This will make it even more hands off for their crew and easier for adjustments.”
Published October 13, 2023